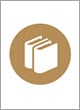
PREN ISO 11137-2 : DRAFT 2009
Superseded
A superseded Standard is one, which is fully replaced by another Standard, which is a new edition of the same Standard.
View Superseded by
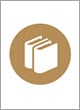
STERILIZATION OF HEALTH CARE PRODUCTS - RADIATION - PART 2: ESTABLISHING THE STERILIZATION DOSE
03-01-2012
01-12-2013
Foreword
Introduction
1 Scope
2 Normative references
3 Abbreviations, terms and definitions
3.1 Abbreviations
3.2 Terms
4 Definition and maintenance of product families
for dose setting, dose substantiation and
sterilization dose auditing
4.1 General
4.2 Defining product families
4.3 Designation of product to represent a
product family for performance of a verification
dose experiment or sterilization dose audit
4.3.1 Product to represent a product family
4.3.2 Master product
4.3.3 Equivalent product
4.3.4 Simulated product
4.4 Maintaining product families
4.4.1 Periodic review
4.4.2 Modification to product and/or manufacturing
process
4.4.3 Records
4.5 Effect of failure of establishment of sterilization
dose or of a sterilization dose audit on product family
5 Selection and testing of product for establishing
the sterilization dose
5.1 Nature of product
5.2 Sample item portion (SIP)
5.3 Manner of sampling
5.4 Microbiological testing
5.5 Irradiation
6 Methods of dose establishment
7 Method 1: dose setting using bioburden information
7.1 Rationale
7.2 Procedure for Method 1 for product with an
average bioburden greater than or equal
to 1,0 for multiple production batches
7.2.1 General
7.2.2 Stage 1: Select SAL and obtain samples of
product
7.2.3 Stage 2: Determine average bioburden
7.2.4 Stage 3: Obtain verification dose
7.2.5 Stage 4: Perform verification dose experiment
7.2.6 Stage 5: Interpretation of results
7.2.7 Stage 6: Establish sterilization dose
7.3 Procedure for Method 1 for product with an average
bioburden greater than or equal to 1,0 for a single
production batch
7.3.1 Rationale
7.3.2 General
7.3.3 Stage 1: Select SAL and obtain samples of
product
7.3.4 Stage 2: Determine average bioburden
7.3.5 Stage 3: Obtain verification dose
7.3.6 Stage 4: Perform verification dose experiment
7.3.7 Stage 5: Interpretation of results
7.3.8 Stage 6: Establish sterilization dose
7.4 Procedure for Method 1 for product with an average
bioburden in the range 0,1 to 0,9 for multiple or
single production batches
8 Method 2: Dose setting using fraction positive information
from incremental dosing to determine an extrapolation factor
8.1 Rationale
8.2 Procedure for Method 2A
8.2.1 General
8.2.2 Stage 1: Select SAL and obtain samples of product
8.2.3 Stage 2: Perform incremental dose experiment
8.2.4 Stage 3: Perform verification dose experiment
8.2.5 Stage 4: Consideration of results
8.2.6 Stage 5: Establish sterilization dose
8.3 Procedure for Method 2B
8.3.1 General
8.3.2 Stage 1: Select SAL and obtain samples of product
8.3.3 Stage 2: Perform incremental dose experiment
8.3.4 Stage 3: Perform verification dose experiment
8.3.5 Stage 4: Consideration of results
8.3.6 Stage 5: Establish sterilization dose
9 Method VD[max] - Substantiation of 25 kGy or 15 kGy as
the sterilization dose
9.1 Rationale
9.2 Procedure for Method VD[max][25] for multiple production
batches
9.2.1 General
9.2.2 Stage 1: Obtain samples of product
9.2.3 Stage 2: Determine average bioburden
9.2.4 Stage 3: Obtain VD[max][25]
9.2.5 Stage 4: Perform verification dose experiment
9.2.6 Stage 5: Interpretation of results
9.2.7 Confirmatory verification dose experiment
9.3 Procedure for Method VD[max][25] for a single
production batch
9.3.1 Rationale
9.3.2 General
9.3.3 Stage 1: Obtain samples of product
9.3.4 Stage 2: Determine average bioburden
9.3.5 Stage 3: Obtain VD[max][25]
9.3.6 Stage 4: Perform verification dose experiment
9.3.7 Stage 5: Interpretation of results
9.3.8 Confirmatory verification dose experiment
9.4 Procedure for Method VD[max][15] for multiple
production batches
9.4.1 General
9.4.2 Stage 1: Obtain samples of product
9.4.3 Stage 2: Determine average bioburden
9.4.4 Stage 3: Obtain VD[max][15]
9.4.5 Stage 4: Perform verification dose experiment
9.4.6 Stage 5: Interpretation of results
9.4.7 Confirmatory verification dose experiment
9.5 Procedure for Method VD[max][15] for a single
production batch
9.5.1 Rationale
9.5.2 General
9.5.3 Stage 1: Obtain samples of product
9.5.4 Stage 2: Determine average bioburden
9.5.5 Stage 3: Obtain VD[max][15]
9.5.6 Stage 4: Perform verification dose experiment
9.5.7 Stage 5: Interpretation of results
9.5.8 Confirmatory verification dose experiment
10 Auditing sterilization dose
10.1 Purpose and frequency
10.2 Procedure for auditing a sterilization dose
established using Method 1 or Method 2
10.2.1 General
10.2.2 Stage 1: Obtain samples of product
10.2.3 Stage 2: Determine average bioburden
10.2.4 Stage 3: Perform verification dose experiment
10.2.5 Stage 4: Interpretation of results
10.2.6 Augmentation of a sterilization dose established
using Method 1, Method 2A or Method 2B
10.3 Procedure for auditing a sterilization dose
substantiated using Method VD[max][25] or VD[max][15]
10.3.1 General
10.3.2 Stage 1: Obtain samples of product
10.3.3 Stage 2: Determine average bioburden
10.3.4 Stage 3: Perform verification dose experiment
10.3.5 Stage 4: Interpretation of results
10.3.6 Confirmatory sterilization dose audit
10.3.7 Augmentation of a sterilization dose
substantiated using Method VD[max][25] or
VD[max][15]
10.4 Failure of the sterilization dose audit
11 Worked examples
11.1 Worked examples for Method 1
11.2 Worked examples for Method 2
11.2.1 General
11.2.2 Worked example for Method 2A (SIP equal
to 1,0)
11.2.3 Worked example for Method 2A (SIP less
than 1,0)
11.2.4 Worked example for Method 2B
11.3 Worked examples for Method VD[max]
11.4 Worked example of a sterilization dose audit for a
dose established using Method 1, the findings from
which necessitated augmentation of the sterilization
dose
11.5 Worked example of a sterilization dose audit for a dose
established using Method 2A, the findings from which
necessitated augmentation of the sterilization dose
11.6 Worked example of a sterilization dose audit for
a sterilization dose substantiated using Method
VD[max][25]
Annex ZA (informative) - Relationship between this International
Standard and the Essential Requirements of EU
Directive 93/42/EEC and 90/385/EEC
Bibliography
Defines methods of determining the minimum dose needed to achieve a specified requirement for sterility and methods to substantiate the use of 25 kGy or 15 kGy as the sterilization dose to achieve a sterility assurance level, SAL, of 10[-6].
Committee |
TC 204
|
DocumentType |
Draft
|
PublisherName |
Comite Europeen de Normalisation
|
Status |
Superseded
|
SupersededBy |
Standards | Relationship |
09/30197784 DC : 0 | Identical |
ISO 11137-1:2006 | Sterilization of health care products Radiation Part 1: Requirements for development, validation and routine control of a sterilization process for medical devices |
ISO 11737-2:2009 | Sterilization of medical devices Microbiological methods Part 2: Tests of sterility performed in the definition, validation and maintenance of a sterilization process |
ISO 11737-1:2006 | Sterilization of medical devices Microbiological methods Part 1: Determination of a population of microorganisms on products |
ISO 13485:2016 | Medical devices Quality management systems Requirements for regulatory purposes |
AAMI TIR27 : 1ED 2001 | STERILIZATION OF HEALTH CARE PRODUCTS - RADIATION STERILIZATION - SUBSTANTIATION OF 25 KGY AS A STERILIZATION DOSE - METHOD VD MAX |
AAMI ST32 : 1991 | GUIDELINE FOR GAMMA RADIATION STERILIZATION |
ISO/TS 11139:2006 | Sterilization of health care products Vocabulary |
ISO 11137-3:2017 | Sterilization of health care products — Radiation — Part 3: Guidance on dosimetric aspects of development, validation and routine control |
ISO 14971:2007 | Medical devices Application of risk management to medical devices |
ISO 11137:1995 | Sterilization of health care products Requirements for validation and routine control Radiation sterilization |
Access your standards online with a subscription
Features
-
Simple online access to standards, technical information and regulations.
-
Critical updates of standards and customisable alerts and notifications.
-
Multi-user online standards collection: secure, flexible and cost effective.