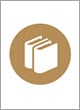
NS EN 415-7 : 2006 + A1 2008
Current
The latest, up-to-date edition.
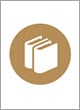
SAFETY OF PACKAGING MACHINES - PART 7: GROUP AND SECONDARY PACKAGING MACHINES
12-01-2013
Foreword
Introduction
1 Scope
2 Normative references
3 Terms and definitions
3.1 Definition of terms
3.2 Description of group and secondary packaging machines
3.2.1 Machines for erecting packaging materials
3.2.2 Product loading/unloading machines
3.2.3 Machines for sealing packages
3.2.4 Group package form, fill and seal machines
4 Hazards on group and secondary packaging machines
4.1 General
4.2 General group and secondary packaging machine hazards
4.2.1 General
4.2.2 Mechanical hazards
4.2.3 Electrical hazards
4.2.4 Thermal hazards
4.2.5 Noise
4.2.6 Hazards from products and materials
4.2.7 Hazards due to neglecting ergonomic principles
4.2.8 Hazards caused by failures
4.2.9 Hazards due to neglecting hygienic design
principles
4.2.10 Common mechanisms on group and secondary
packaging machines
4.3 Hazards associated with a tray erecting machine
4.3.1 General
4.3.2 Tray blank magazine
4.3.3 Tray blank extracting mechanism
4.3.4 Tray blank transport mechanism
4.3.5 Forming assembly
4.3.6 Discharge mechanism
4.4 Hazards associated with case erecting machines
4.4.1 General
4.4.2 Hazards associated with a semi-automatic
case erector
4.4.3 Hazards associated with a fully automatic
case erector
4.5 Hazards associated with a place packing machine
4.5.1 General
4.5.2 In-feed conveyor
4.5.3 Product collating mechanisms
4.5.4 Transport mechanism
4.5.5 Product loading mechanism
4.6 Hazards associated with a horizontal case loading machine
4.6.1 General
4.6.2 Product in-feed conveyor
4.6.3 Product turning devices
4.6.4 Product collating mechanism
4.6.5 Case loading mechanism
4.6.6 Case funnel
4.6.7 Case support arms
4.6.8 Discharge conveyor
4.7 Hazards associated with case taping machines
4.7.1 General
4.7.2 Hazards associated with a manually adjusted case
taping machine without flap tucking
4.7.3 Hazards associated with a self adjusting case taping
machine without flap tucking
4.7.4 Hazards associated with a manually adjusted case
taping machine with flap tucking
4.7.5 Hazards associated with a fully automatic case
taping machine
4.8 Hazards associated with a wraparound case packing machine
4.8.1 General
4.8.2 Case blank magazine
4.8.3 Product in-feed conveyor
4.8.4 Transport mechanism
4.8.5 Case erecting mechanism
4.8.6 Product loading mechanism
4.8.7 Flap tucking mechanisms
4.8.8 Case closing devices
4.8.9 Case compression
4.8.10 Discharge conveyor
5 Safety requirements and measures for group and secondary
packaging machines
5.1 General
5.2 General requirements for group and secondary packaging
machines
5.2.1 General
5.2.2 Requirements to eliminate mechanical hazards
5.2.3 Electrical requirements
5.2.4 Thermal hazards
5.2.5 Noise reduction
5.2.6 Measures to control hazards generated by products
and materials
5.2.7 Ergonomic design principles
5.2.8 Requirements to prevent hazards caused by failures
5.2.9 Hygienic design requirements
5.2.10 Requirements for mechanisms used on most group
and secondary packaging machines
5.3 Safety requirements for a tray erecting machine
5.3.1 General
5.3.2 Tray blank magazine
5.3.3 Tray blank extracting mechanism
5.3.4 Tray blank transport mechanism
5.3.5 Forming assembly
5.3.6 Discharge mechanism
5.4 Safety requirements for a case erecting machine
5.4.1 Safety requirements for a semi-automatic
case erector
5.4.2 Safety requirements for a fully automatic
case erector
5.5 Safety requirements for a place packing machine
5.5.1 General
5.5.2 In-feed conveyor
5.5.3 Product collating mechanisms
5.5.4 Transport mechanism
5.5.5 Product loading mechanism
5.6 Safety requirements for a horizontal case loading
machine
5.6.1 General
5.6.2 In-feed conveyor
5.6.3 Product turning devices
5.6.4 Product stacking mechanism
5.6.5 Case loading mechanism
5.6.6 Case funnel
5.6.7 Case support arms
5.6.8 Discharge conveyor
5.7 Safety requirements for case taping machines
5.7.1 Safety requirements for a manually adjusted
case taping machine without flap tucking
5.7.2 Safety requirements for a self adjusting case
taping machine without flap tucking
5.7.3 Safety requirements for a manually adjusted case
taping machine with flap tucking
5.7.4 Safety requirements for a fully automatic case
taping machine
5.7.5 Noise reduction
5.8 Safety requirements for a wraparound case packing
machine
5.8.1 General
5.8.2 Case blank magazine
5.8.3 In-feed conveyor
5.8.4 Transport mechanism
5.8.5 Case erecting mechanism
5.8.6 Product loading mechanism
5.8.7 Flap tucking
5.8.8 Case closing devices
5.8.9 Case compression
5.8.10 Discharge conveyor
6 Verification of safety requirements and measures
6.1 General
6.2 Visual inspections with the machine stopped
6.2.1 Mechanical parts
6.2.2 Pneumatic systems
6.2.3 Hydraulic systems
6.2.4 Electrical systems
6.2.5 Guards
6.2.6 Design requirements
6.3 Measurements with the machine stopped
6.3.1 Guards
6.3.2 Electrical testing
6.4 Visual inspections with the machine running
6.4.1 Guards
6.4.2 Interlocking devices
6.4.3 Dissipation of stored energy
6.5 Measurements with the machine running
6.5.1 Measurement and declaration of noise emission
6.5.2 Temperature
6.6 Verification procedures
7 Information for use
7.1 Markings
7.2 Signals and warning signs
7.3 Instruction handbook
7.3.1 General
7.3.2 Requirements specific to group and secondary
packaging machines
Annex A (normative) Noise test code for group and secondary
packaging machines - grade of accuracy 2 and 3
Annex B (normative) Methods of safeguarding small and medium
sized apertures
Annex C (normative) Methods of safeguarding large apertures
Annex D (normative) ESPE Muting
Annex ZA (informative) Relationship between this European
Standard and the Essential Requirements of EU
Directive 98/37/EC
Bibliography
Deals with safety requirements for machine design, construction, installation, commissioning, operation, adjustment, maintenance and cleaning of group and secondary packaging machines.
DevelopmentNote |
2006 Edition Re-Issued in November 2008 & incorporates AMD 1 2008. (11/2008)
|
DocumentType |
Standard
|
PublisherName |
Norwegian Standards (Norges Standardiseringsforbund)
|
Status |
Current
|
Standards | Relationship |
UNE-EN 415-7:2007 | Identical |
DIN EN 415-7:2009-12 | Identical |
EN 415-7:2006+A1:2008 | Identical |
I.S. EN 415-7:2006 | Identical |
BS EN 415-7 : 2006 | Identical |
UNI EN 415-7 : 2008 | Identical |
Access your standards online with a subscription
Features
-
Simple online access to standards, technical information and regulations.
-
Critical updates of standards and customisable alerts and notifications.
-
Multi-user online standards collection: secure, flexible and cost effective.